Quality Management
Our main Goal is customer’s satisfaction. In order to accomplish this we are doing our best during whole process from production to sale including after market service.
"Pump Quality is Everything "
As we all know, slurry pumps and spare parts must perform at high levels of efficiency and durability. Poor quality can result in frequent breakdowns, higher maintenance costs, and lower productivity. On the other hand, high-quality slurry pumps and spare parts are built to last, providing reliable and efficient performance, which can result in reduced downtime, lower maintenance costs, and improved productivity.
#1 Metallographic analysis
Our furnace material elements testing adopts the most advanced material inspection equipment—Original Germany spectrometer to ensure the material ratio meeting standard slurry pump requirement.
And we control strictly every process to guarantee that perfect pump and spare parts will be produced.


#2 Pump hardness Testing
Hardness is one of the key properties that determine the resistance of the materials to wear and abrasion. It is performed during the production of slurry pumps to ensure that the materials used in their construction meet the required standards and specifications, and to assess the ability of the pumps to perform at high levels of efficiency and durability in demanding applications.
#3 Dynamic Balance Testing
Dynamic balance testing is an important step in the production process because it helps to ensure that the pump will perform at optimal levels and meet the requirements of the intended application. Pumps that are not properly balanced can experience excessive vibration and wear, which can lead to premature failure and increased maintenance costs.
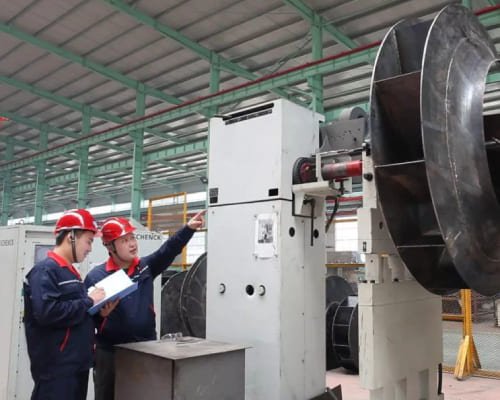
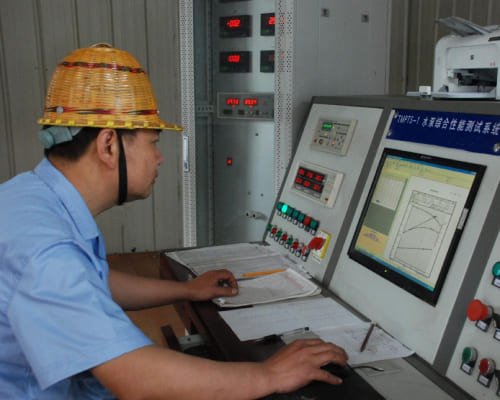
#4 Pump Peformance Testing
By testing the pump on a pump station, manufacturers and operators can identify any potential issues with the pump, such as vibration, cavitation, or overheating, and make necessary adjustments to improve its performance. Testing on a pump station can also help to ensure that the pump meets the required safety and performance standards, and can provide valuable information for maintenance and troubleshooting in the future.
Quality Improvement
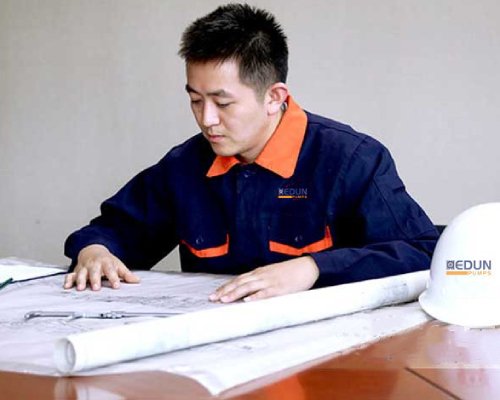
Custom Design and Material Selection
Hedunpumps engineer will develop the pumps construction when our standard pump could not meet your Special parameters, for example, cut the impeller blades to get a higher head.
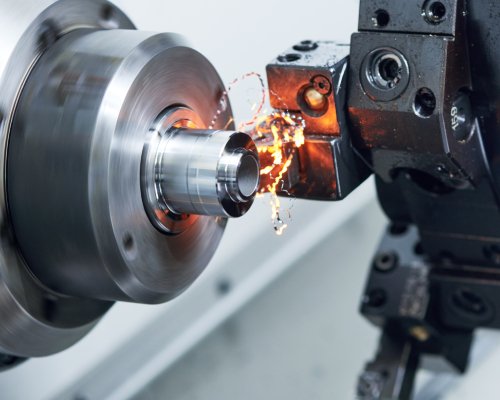
Accurate Manufacturing Processes
Adopting high precision machining and assembly to ensure that the pump components are accurately manufactured and assembled,resulting in improved efficiency and durability.

All Dimensions Testing
Hedunpumps conduct thorough testing at various stages of the production process, including hardness testing, dynamic balance testing, and performance testing, to ensure meet all your needs

Customer Feedback
We regularly gather feedback from customers and users of the pumps, these provide valuable insights into the performance of the pumps in actual use, and help us to identify areas for improvement.