Mine Tailings Pump Applications
Mining Pumps Overview Video
Hedunpumps keeps a complete product range that will satisfy even the toughest needs for the mining industry. We have a premium pump for every mining application. Whether it’s coarse grit and abrasives, high head requirements, slurry transfer, water supply and boosting, we have a pumping solution that will excel in performance. Our mining pump experts specialize in meeting the high demands of pumping corrosive water, slurry transfer, waste water and tailing transfer, grit and abrasives, high pressure pumping, rapidly changing water levels and any factors that are specific to mining.
Mining Pumps Main Applications
In the mining and mineral processing industries, our slurry pumps are designed to handle harsh liquids, slurry, sludge and other abrasive materials.
- Underground Mining
- Abrasive Sludge Dewatering
- Froth Flotation
- Slurry Transfer
- Water Supply
- Water Boosting
- Surface Mining
- Mill Thickener
- Coal Prep
- Aggregate Processing
- Water Transfer Application
- Fine Primary Mill Grinding
- Solid Handling
- Tailing
- Mineral Processing

Introduction of Slurry Pump For Mining: Problems & Solution
Mining slurry pumps include high chrome alloy slurry pumps, submersible slurry pumps, rubber lined slurry pumps and so on. As an indispensable auxiliary equipment in the beneficiation plant, the role of mining slurry pump should be paid high attention. They are widely used in grinding, screening, magnetic separation, flotation, after the raw ore slurry, concentrate ore slurry or tailing ore slurry and other conveying work.
The centrifugal force of slurry pump allows the solid-liquid mixed slurry to reach the designated operating point. The solid particles in the material award will produce continuous impact and abrasion on the pump body, in addition, strong acid, strong alkali slurry will also produce chemical corrosion of the pump body, these are seriously affect the service life of the slurry pump.
Take the flotation process as an example, after grinding the solid-liquid combination of raw ore slurry will be slurry pump transported to the hydrocyclone and other screening equipment. A part of the concentrate goes into flotation operation, and the flotation out of the concentrate will be transported to the pump box first, and then through the slurry pump of the mine, the concentrate will be transported to the thickener for dewatering operation. The remaining tailings from flotation are discharged into the tailings pump box and then discharged via slurry pumps to the tailings dry discharge operation or directly to the tailings storage.

The selection of each stage is not quite the same, and if the selection is not good, it will greatly reduce the overall efficiency of the selection
The overall operating efficiency, resulting in the loss of processing plant. On the choice of mining slurry pump model, we should pay attention to the following aspects should first clarify the basic parameters of the process slurry pump: flow rate, head and PH value etc. Head is the energy obtained by the pump per unit weight of fluid. Flow rate is the amount of slurry liquid excluded per unit time. The head and flow rate then determine the specific model and size of the slurry pump. It is also necessary to clarify the solid-liquid ratio, particle condition, because it has a high reference value in slurry pump selection.
The next consideration is used after above process. Is it after the grinding process, or after the flotation process with chemicals? Abrasion or corrosion resistance generally we will consider, relatively speaking, used in flotation or other mineral processing with chemicals after the process, concentrate than tailings of the relatively small amount of chemicals, so both of these in the wash type when the external tailings slurry pump needs a high corrosion resistance.
There are some other factors, such as flotation out of the concentrate, with a certain proportion of froth. This is also the slurry pump selection needs to consider factors, if the flotation of the concentrate after the foam content is high, may consider the use of special froth slurry pump, this slurry pump is specially designed and produced for the flotation process. Another is after hydrocyclone, hydrocyclone classification relies on centrifugal force, the greater the feed pressure, the higher the pulp flow rate, the greater the rotational speed of the pulp and centrifugal force, then the better the effect of classification, the production efficiency will be improved. The higher the feed pressure depends on the slurry pump.
Problems
Mining operations can face several pumping problems, which can affect the overall efficiency and productivity of the mining process. Here are some common pumping problems in the mining industry and their solutions:
Hedun's Solutions
#1 Cavitation-Cavitation Occurs when pump suction pressure is too low and flow rate is to low to cause liquid to vaporize and form bubbles.
Solution: Increase the pump suction pressure,increase the flow rate or reduce the speed of the pump.
#2 Abrasion -Abrasion cause wear and tear on the pump components.
Solution: Use slurry pumps made from abrasion resistant material
#3 Clogging -Pump or pipeline will be clogged when pumping liquids containing solid particles, such as mud or sludge
Solution: Use pumps with a large enough passage to handle the solids or to install a pre-filter to remove solid particles before they reach the pump.
#4 Corrosion-Pumps or pipeline will be damaged when pumping corrosive liquids, such as acidic or alkaline solutions.
Solution:Use pumps made from corrosion-resistant materials.
#5 Overheating -Overheating can occur when the pump is running for extended periods, causing it to overheat and shut down.
Solution: Install cooling systems, such as water jackets or cooling fans, to dissipate heat, or to reduce the running time of the pump.
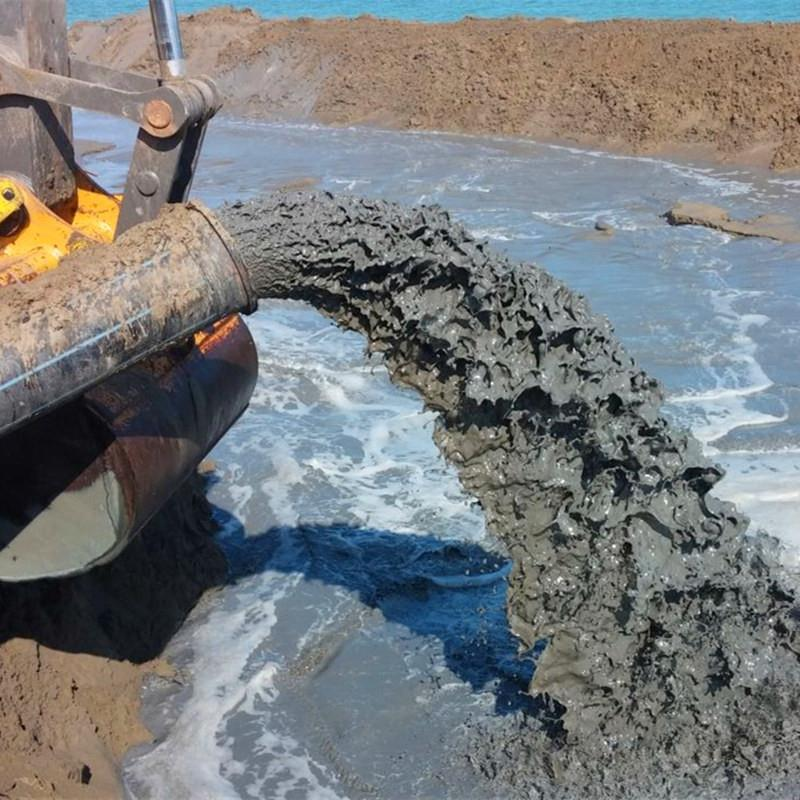
Choosing high quality slurry pumps and spares are very important for pump service life. Furthermore, selecting ideal pump model and power end by professional engineers is also an important aspect to improve the efficiency and reliability of your mining operations.
Tell us about your project. Let’s start the first step of a quote to determine if your project is a fit for our equipment.
Benefits of Using Hedun Mining Pumps
#01 Increase efficiency
Hedun Slurry pumps are designed to move dense and abrasive fluids, such as slurries, more efficiently than other types of pumps. By using our slurry pumps, mining operations can reduce the amount of energy required to move these fluids, leading to greater efficiency and cost savings.
#02 Cost-saving
Hedun Slurry pumps can help reduce costs in several ways. By improving efficiency, they can lower energy consumption and reduce maintenance requirements. In addition, their durability and long service life can reduce your need for frequent replacements or repairs, further reducing costs over time.
#03 Customizability
Our Slurry pumps can be customized to meet the specific needs of a mining operation. This includes choosing the right flow rate, pressure, and other specifications to match the particular type of slurry being pumped. By selecting the right pump for your project, mining operations can improve efficiency and reduce costs.
#04 Durability
Our Slurry pumps are designed to withstand the harsh operating conditions commonly found in mining operations. This includes resistance to wear and tear from abrasive materials and protection against corrosion from chemical exposure. As a result, Hedun slurry pumps have a longer service life than many other types of pumps, reducing maintenance and replacement costs.